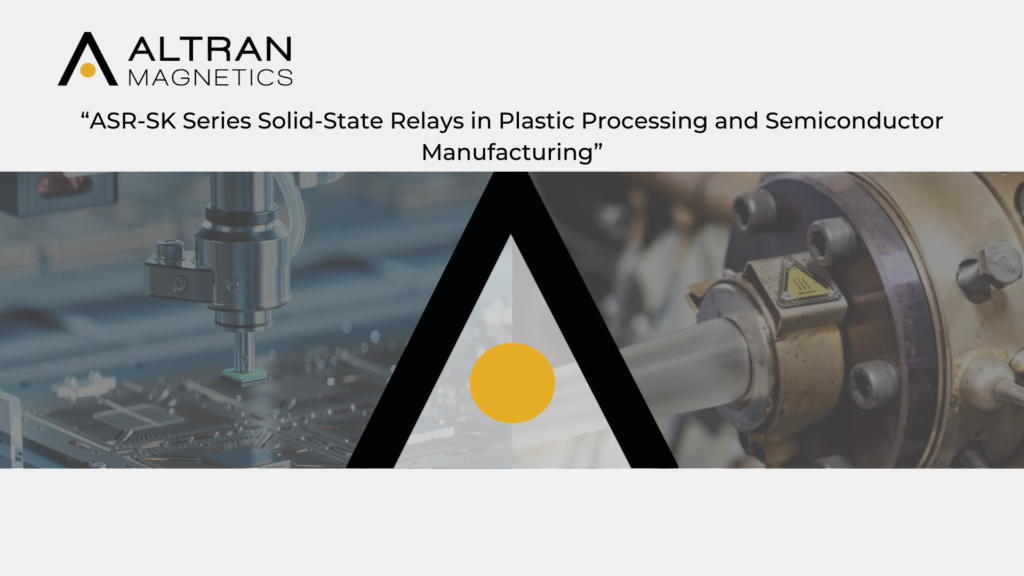
ASR-SK Series Solid-State Relays in Plastic Processing and Semiconductor Manufacturing
Precision, reliability, and efficiency are essential in industries like plastic processing and semiconductor manufacturing, where equipment must handle varying loads and temperature-sensitive processes. The ASR-SK